This already looks a lot better. For an arduino nano (which is a relatively old fashioned / old technology microcontroller) it does not matter very much and this looks āacceptableā.
However, if you want to use this as an exercise in optimizing the PCB there is still room left for improvement. For example, the green track below can easily be routed on the red layer, so there is a more continuous GND below that group of tracks:
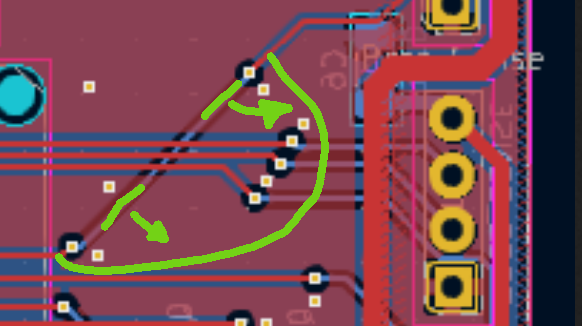
When there is no possibility to do such things, you should still optimize the GND plane by moving the viaās closer to the track to reduce the opening in the GND pane and the size of the detour the current through the GND plane must make.
I see that youāve placed some viaās in strategic positions. In the corner of planes to stitch them, and near viaās in signal lines. This is good, but you have not done this everywhere and you can do some more of these. Viaās are essentially free (unless you really have an excessive amount of them).
These two parts of your GND plane are open on one end. Such tracks can sometimes act as an antenna and that is not good.
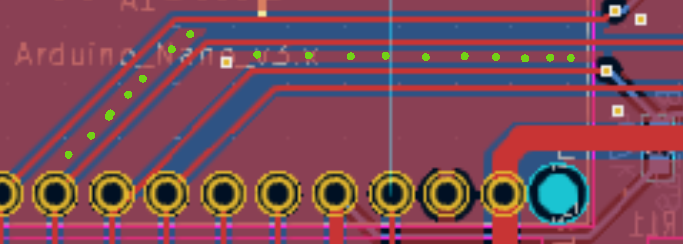
The track with these green dots can also be moved to the red layer.
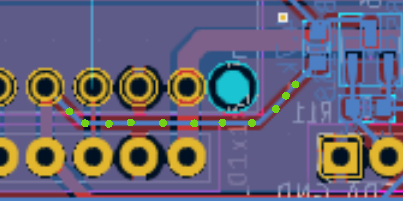
In general itās common practice to place the (main) GND plane on the opposite layer then the SMT footprints, so you also have a continuous GND plane under all the SMT footprints. This also reduces the amount of vias (routing effort) because signals are routed on the same layer as the SMT footprints. Especially in the area around the barrel jack you are loosing a bit of the GND reference because itās on the same layer as the SMT tracks. Now you have a viaās in (nearly) all signal lines which are leaving a group of SMT footprints. There is no need to change this now, but something to consider for your next PCB.
What is this big rectangular thing?
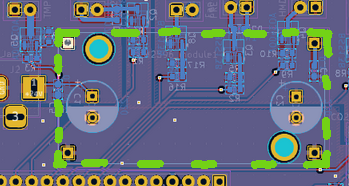
I guess itās such a chinese SMPS module.
You already have a few electrolytic capacitors āsticking thoughā it. and mounting holes (are they for that module?
You can put SMT footprints under modules such as the arduino and (presumed) SMPS module. But do note that this makes it more difficult to do rework and repairs.
Some things to consider for all PCBās: Add mounting holes to your project. Corners are not the ideal locations for mounting holes. The best locations are near connectors, especially screw terminals because those are locations where mechanical stress is introduced in to the PCB.
Put your name, date and project name on the PCB. Itās always nice to see a bit of promotion of KiCad (KiCad has some footprints with logos) and some text so you donāt forget (years later) which project (or which variant / revision of a project) it is is useful. When you want to make your project public, itās also easier for others who see the PCB to find more info. For commercial projects you may also need other icons such as RoHS or the garbage can.