I can not do a decent board review from a few screenshots.
Even though you say your modules have built-in decoupling capacitors, I would still add more decoupling capacitors. Especially with high current devices such as motor drivers.
The decoupling capacitors are not only used to smooth the power supply to IC’s, they are also for smoothing the electrical noise that IC’s generate when switching and preventing it from reaching other circuitry.
What is the current capacity of your motors? It’s probably not strictly needed, but I would still add an extra via in the high current motor tracks (and power supply tracks). Via’s are cheap, you also have plenty of room. Have you used the PCB calculator (or a table) to make sure your track widht is adequate for your motor drivers?
Motor drivers (and any high current switchers) also do not only need decoupling capacitors, they also need buffer capacitors. These are usually bigger, but cheaper electrolytics in the range of 100uF to 1000uF (or even bigger especially for big motors). 2 electrolytics of 220uF each are usually better than one big capacitor of 470uF. But to be sure you have to check the ESR value from the datasheet.
In this area your GND plane is very narrow. If it is a spot which has high motor currents, then make it wider.

You should be aware of how the currents flow through the GND plane. Print out the PCB bottom on a piece of paper (preferably enlarged scale) and draw the main current paths through the GND plane on the paper.
Keep as much of the tracks on the top of the PCB, and make cuts in the GND plane as small as possible. This reduces emitted EMI noise, and also lowers voltage differences over the GND plane.
Why do you have 4 SMD resistors and 16 THT resistors?
The THT resistor also look smaller then the “most common” size. Are you sure they are the right size?
If this is to fit on an “arduino” board with a big square USB-B connector, then you have very little clearance between the top of the connector and the bottom of the PCB. There is no room left for pins of IC’s and connectors sticking out in that area. If you can not move the connectors, then cut of the pins before you put those components in the PCB. Make them so short that they do not stick out of the PCB.
Also put a few layers of insulation tape, plastic foil or cardboard between the metal USB connector and your PCB to prevent any possibility for shorts.
Where does power for the “arduino” board come from?
How is power routed?
What happens if the “arduino” has power, but this PCB does not (or vise versa).
You should not apply logic signals to IC’s that do not have a working power supply.
Apart from these remarks. Your board looks a lot better than I’m expecting for a first design. You have for example even thought about lowering GND plane impedance by making some bridges over high current tracks:
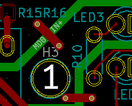
But why not simply move those tracks to the top layer, and have a continuous GND plane?