- Draw the schematic (partly)
I think any EDA allows drawing the schematic partly. 
- Define new parts in the schematic library, and link them 1-to-1 to their footprints.
Can do. In KiCad symbols and footprints are separate. You attach a footprint to the symbol. You can have generic symbols withouth footprints so that you attach the footprint after you have placed the symbol to the schematic, or you can have fully defined symbols with pre-attached footprints. You can change the attached footprint at any time.
- Define the needed footprints, including extra layers for milling and engraving of the front panel.
Here are layers in the footprint editor:
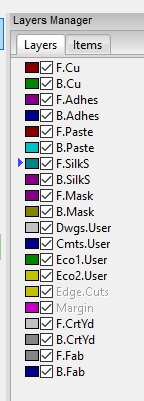
- Use Freecad to draw more-than-trivial 3d models, and export them to step.
Even better, you can add the kicadStepUp workbench and collaborate between FreeCAD and KiCad.
- Import the step file into the footprint, so collisions are detected in 3d.
There’s no collision detection in KiCad’s 3D viewer except your eyes. Otherwise, yes.
- Finish drawing the schematic.
Schematics are never finished. 
- Create a new PCB from template, and import the schematic into it.
Describe “template”. KiCad has template projects, but I suspect you mean something different.
- Copy-and-paste fragments of other PCB’s into the board and the schematic.
That was discussed already a bit. You can have hierarchical schematic sheets and copy them to your project. Full copypaste isn’t implemented between schematics in the stable v5.1. So, basically yes, although not identically to Altium I presume.
- Arrange the components, so the air wires are not crossing each other too much. Select groups of components in the schematic, and grab that group of components in the PCB (cross probing)
At the moment cross-probing works for one component at a time, or you can selects footprints which belong to the same hierarchical sheet. Cross probing a selection from schematic has been promised for v6.
- Change my mind about some components, and change the schematic.
I do (or actually my boss does) that all the time. Changing one’s mind is easy. Changing the schematic, too.
- Import the changes made in the schematic into the PCB.
Of course.
- Draw the copper traces
Yes, with the help of Push’n’Shove router.
- Pour the ground plane, stitch it with via’s in a random pattern
KiCad uses zones (fills) for planes. There’s no automated via stitching, you just add vias manually. I’m not sure if there exists any python script for that.
- Move traces around, so the ground planes are more “solid”, less loop area.
Bread and butter.
- Re-annotate the PCB board, so all the designators change.
As easy as any other change if done from schematic. Automatic annotation from PCB (geographical reannotation) is under work for v6.
- Move the designators around on the silkscreen, so they are all visible.
Before this you want to learn to use the Layer Manager Layers and Items to help you see only what you need. Standard work for every board.
- Update the schematic, so all the designators are in sync again.
See 15 above.
- Add extra layers to the PCB, so the front panel can be made by the CNC mill or the laser engraving machine.
There are free layers and more are coming in v6.
- Add texts to the silkscreen (like part number, hints what signals have to be connected where and so on)
You can add text items to any layer.
- Run a design rule check.
Yes, one of the most important parts of an EDA.
- Use a output job file to generate the following documents in one go:
Gerber files
Drill file
DXF file with all layers
Pick and place file (excel file with one line per part with x,y,rotation, designator, and so on)
BOM file (excell file with one line per unique part, with ordernumbers, quantity, and so on)
PDF with only the layers so I can etch a PCB myself (it is seldom used, but I like to have it generated just in case)
Unfortunately not in one go. These can be done one by one. There has been preliminary developer talk about something like better management of output tasks.
- Put the Gerber and drill files into a zip file, and send it to a PCB manufacturer (if I want to assemble myself)
Must be done manually.
- Put the Gerber, drill file, pick and place file and bom file into a zip file, and send it to a manufacturer (so I don’t have to do anything anymore, just pay and wait for assembled boards to arrive)
Likewise.
- Change the font size in the .dxf file (I’ve written a small program that does this), so it matches the font used in Autocad, and use the laser engraving machine to generate a front panel.
- Use the .dxf file to drive the CNC machine to mill holes in the case.
Out of scope for KiCad, but you knew that already.