Hi,
for my current project I need several copper planes in arc form.
I know KiCad is not offering the possibility to make circles or arcs with the copper layer. The workaround for me would be to manually make a copper zone and drag the edges until the desired shape is nearly reached. But this would be a very time consuming and not a very satisfying solution.
Does anybody has a better approach for this?
I canât give you a direct solution, but PCBnew does support python scripting. I could imagine you could make a simple script that drew arcâd polygons, that script may even already exist, I am just not sure where.
Hope this helps at least a little.
At the moment one option is to write an external program/script which generates a series of filled polygons in a format which KiCad understands and will render. Will you need to create an electrical connection to the pattern, and how do you plan to do it? If you place a single pad, then generate a filled zone pattern to cut/paste into the pcb file, you can get an electrical connection. You would need to play around a little. See if you can create filled zones with voids, then write the software to generate the pattern you need.
Another option is to create a bitmap file with a resolution of at least 0.05mm and use the âbitmap2cmpâ tool to create a footprint module which contains the pattern. If you know the PostScript language you can define the pattern very well.
One way of potentially doing this is to import the file as a DXF drawing, then save and close the file. Open the board file in a text editor and change the layer from board outline to Cu.F save and reopen it should now be on the coper layer.
@asobernewt very interesting approach, I tried it but KiCad is recognizing this and says that it is a wrong layer for this type of drawing (arc) and the second thing is, that it is not possible to assign the arc to the desired net⌠But due to your suggestion I was looking into the pcb file and found some interesting information of a simple polygon I have drawn earlier:
(zone (net 2) (net_name GND) (layer F.Cu) (tstamp 0) (hatch edge 0.508)
(connect_pads (clearance 0.2))
(min_thickness 0.254)
(fill yes (arc_segments 32) (thermal_gap 0.508) (thermal_bridge_width 0.508))
(polygon
(pts
(xy 173 109) (xy 173 114) (xy 169 114) (xy 169 109)
)
)
)
So basically a polygon consist of simple xy coordinates of all corners. In this case, as @Ldoiron17 mentioned, the best way would be to write a script that draws the arced polygon. My main problem is that I am not very good at programming in python so I will search the net if such a script is already existing. The best thing would be a script that takes a dxf file and converts it into a polygon with the same shape (the net assignment could be done by hand later on).
PS: I also tried @cbernardoâs proposal but I didnât worked out very well.
PPS: If anybody is willing to program this script/program I would be very thankful and I guess some of the community members as well
[quote=âsuckiden, post:5, topic:1229â]
PPS: If anybody is willing to program this script/program I would be very thankful and I guess some of the community members as wellâŚ[/quote]
Here you go, pretty crude but did work for me already.
Runs on Python 2.7.2 and goes into a xyz.kicad_pcb via text-editor (I have KiCAD BZR5978).
KiCAD_CopperArc.py on Github Gist
The script pproduces the segments for an arc with the following specs (can be adjusted in the script):
- Center = x 105.0 mm / y 105.0 mm
- Radius = 20 mm
- Sides = 36
- StartAngle = 45.0 degrees
- Angle = 135.0 degrees
- TrackWidth = 0.4 mm
- Layer = F_Cu
- Net = 0
KiCAD has got some mind of itâs own in regards to nets of stuff you add to a kicad_pcb file thatâs not originally from KiCAD (been there, had lotâs of fun) - it needs some fiddling and determination until it works (I suggest to get a proper file with nets from eeschema and adding to that) and the new copper is accepted and stays on the net you gave it, but once you got it - itâs working
PS: totally forgot, I naturally used that script for something else and pulled it out of something bigger⌠looking around youâll notice it is able do a bit more than just drawing lines to form an arc if correctly adjusted. Iâve already used it for pretty complex outlines/millings/comments/coppertraces/etc⌠that were based on calculations.
Hey, thank you for the script. Sounds like this is exactly was I was looking for
I tried to run the script in the command shell and I can see the output in the command line:
but I donât get the output file as you described. Did I missed anything?
I used that just as a âquick hackâ and had to modify the code all the time to get the output I wanted/needed, so it appeared in the python console in my WingIDE and from there it was just copy&paste into the kicad_pcb.
If I run it in command line in windows the following way:
E:\Data_Code\Python\KiCAD_CopperArc>KiCAD_CopperArc.py > CopperArc.txt
the result will be in CopperArc.txt and you can copy&paste from there?
hi,
finally got it up and running the result looks like this:
but how do I get from there to a pad that looks like this:
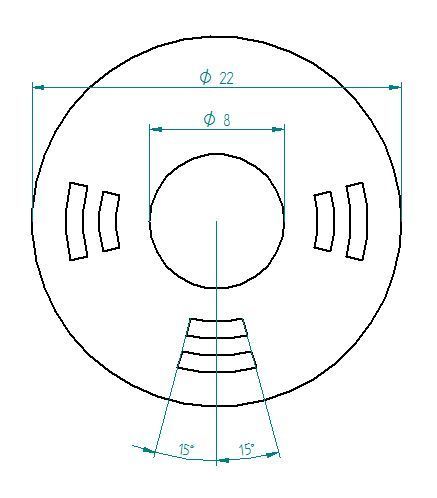
even drawing two arcs and connect them with two straight lines will not give me a solid copper plane. Do you think the script can be modified to fit the xy format of a polygon?
(pts
(xy 167.64 90.17) (xy 172.72 90.17) (xy 172.72 93.98) (xy 167.64 93.98)
)
because then I would have a solid plane that can be assigned to a net I want.
thanks for your effort!
Try this oneâŚ
KiCAD_CopperFillPoly.py on Github Gist
It needs a premade polygon/fill area where you replace the polygon and filled_polygon parts. My KiCAD didnât want to fill the area unless I had the net really connected to it with a pad or some wire, thus I also let it output the filled_polygon part so you donât panic - but this doesnât survive a âFill or Refill All Zonesâ commandâŚ
You need to figure out how to get the refill to work though, as for those holes you either have to program them into the output (I wonât be doing that, sorry) or you have to let KiCAD do the work, but for that it needs some net connected to the filling area via pad or wire of the same net being in the to-be-filled-area.
But itâs not that hard anyway, a simple DIY SMD pad with just 1 pin and that being on the GND net will be the easiest (start in eeschema for that one to get the netlist right).
Almost there
I tried the script and it just needs some minor modifications to fit my needs. Currently the script is just drawing one arc:
but I would need to have the option to define a innerRadius and a outerRadius to get the pad shape. The calculation will stays the same but the for loop that calculates the coordinates must run a second time with the other radius value.
I did this manually and it turned out like this:
there is just one thing you need to consider, the coordinates of the second arc needs to be in reverse order to get the shape right. Otherwise it will turn out like this:
I guess this modification can be done very quickly, but if you donât want to spend time on this I will try it by my own.
Anyway thank you for your effort, you already helped me a lot.
cheers!
To go the other way round you probably need to add a minus in front of the i and you would need to adjust the startangle value with the angle value :
pointX = baseX + radius * math.sin(math.radians(sideangle*(-i+0.5) + (startangle - angle)) pointY = baseY + radius * math.cos(math.radians(sideangle*(-i+0.5) + (startangle - angle))
Yeah, will get you there, didnât test it, donât intend to, good luck
Hey Joan,
I finally was able to made the necessary changes and it works like a charm
KiCAD_CopperFillPoly.py (1.6 KB)
import sys, os
import shutil
import math
LIST_pts = [" (polygon\n (pts\n (xy â,â (filled_polygon\n (pts\n (xy â,â) (xy â,â)\n )\n )"]
def FNC_poly (cntr, # (x,y)
innerRadius,
outerRadius,
sides,
startangle,
angle,
):
STR_data = "" baseX = cntr[0] baseY = cntr[1] sideangle = angle / sides
for i in range(sides): pointX = baseX + innerRadius * math.sin(math.radians(sideangle*(i+0.5) + startangle)) pointY = baseY + innerRadius * math.cos(math.radians(sideangle*(i+0.5) + startangle)) STR_data += "{:.4f}".format(pointX) + " " + "{:.4f}".format(pointY) + LIST_pts[2] for i in range(sides): pointX = baseX + outerRadius * math.sin(math.radians(sideangle*((sides-i-1)+0.5) + startangle)) pointY = baseY + outerRadius * math.cos(math.radians(sideangle*((sides-i-1)+0.5) + startangle)) STR_data += "{:.4f}".format(pointX) + " " + "{:.4f}".format(pointY) + LIST_pts[2] STR_data = STR_data[:-6] + LIST_pts[3] return LIST_pts[0] + STR_data + "\n" + LIST_pts[1] + STR_data
if name == âmainâ:
Center = [100.0,100.0] # x/y coordinates of the centre of the pcb sheet innerRadius = 6 # mm outerRadius = 7.5 # mm Sides = 20 StartAngle = 75.0 # degrees Angle = 30.0 # degrees
print FNC_poly (Center, innerRadius, outerRadius, Sides, StartAngle, Angle, )
thank your for your help!
I also want to provide a short how to for other people using this script.
1. open the script with the editor of your choice and change the parameters innerRadius, outerRadius, Sides, StartAngle and Angle to your needs. Save it!
2. under windows, navigate to the folder where the python script is stored and use the command: yourPythonScriptName.py > yourDesiredOutputFile.txt
to get the output data stored in a text file
3. open your PCB file and draw a simple polygon (shape doesnât matter here) save it and close it
4. open your .kicad_pcb file with an editor and detect the polygon youâve drawn earlier, this looks something like this:
(zone (net 1) (net_name +3V3) (layer F.Cu) (tstamp 0) (hatch edge 0.508)
(connect_pads (clearance 0.2))
(min_thickness 0.254)
(fill yes (arc_segments 32) (thermal_gap 0.508) (thermal_bridge_width 0.508))
(polygon
(pts
(xy 105.8154 101.4769) (xy 105.8521 101.3242) (xy 105.8847 101.1705) (xy 105.9133 101.0161) (xy 105.9379 100.8610) (xy 105.9584 100.7052) (xy 105.9748 100.5490) (xy 105.9872 100.3924) (xy 105.9954 100.2356) (xy 105.9995 100.0785) (xy 105.9995 99.9215) (xy 105.9954 99.7644) (xy 105.9872 99.6076) (xy 105.9748 99.4510) (xy 105.9584 99.2948) (xy 105.9379 99.1390) (xy 105.9133 98.9839) (xy 105.8847 98.8295) (xy 105.8521 98.6758) (xy 105.8154 98.5231) (xy 107.2692 98.1539) (xy 107.3151 98.3448) (xy 107.3559 98.5368) (xy 107.3917 98.7299) (xy 107.4224 98.9238) (xy 107.4480 99.1185) (xy 107.4685 99.3137) (xy 107.4839 99.5095) (xy 107.4942 99.7056) (xy 107.4994 99.9018) (xy 107.4994 100.0982) (xy 107.4942 100.2944) (xy 107.4839 100.4905) (xy 107.4685 100.6863) (xy 107.4480 100.8815) (xy 107.4224 101.0762) (xy 107.3917 101.2701) (xy 107.3559 101.4632) (xy 107.3151 101.6552) (xy 107.2692 101.8461)
)
)
)
5. open the output text file of the script and copy the section (ptsâŚ) looks something like this:
(pts
(xy 105.8154 101.4769) (xy 105.8521 101.3242) (xy 105.8847 101.1705) (xy 105.9133 101.0161) (xy 105.9379 100.8610) (xy 105.9584 100.7052) (xy 105.9748 100.5490) (xy 105.9872 100.3924) (xy 105.9954 100.2356) (xy 105.9995 100.0785) (xy 105.9995 99.9215) (xy 105.9954 99.7644) (xy 105.9872 99.6076) (xy 105.9748 99.4510) (xy 105.9584 99.2948) (xy 105.9379 99.1390) (xy 105.9133 98.9839) (xy 105.8847 98.8295) (xy 105.8521 98.6758) (xy 105.8154 98.5231) (xy 107.2692 98.1539) (xy 107.3151 98.3448) (xy 107.3559 98.5368) (xy 107.3917 98.7299) (xy 107.4224 98.9238) (xy 107.4480 99.1185) (xy 107.4685 99.3137) (xy 107.4839 99.5095) (xy 107.4942 99.7056) (xy 107.4994 99.9018) (xy 107.4994 100.0982) (xy 107.4942 100.2944) (xy 107.4839 100.4905) (xy 107.4685 100.6863) (xy 107.4480 100.8815) (xy 107.4224 101.0762) (xy 107.3917 101.2701) (xy 107.3559 101.4632) (xy 107.3151 101.6552) (xy 107.2692 101.8461)
)
6. go to your kicad_pcb file and replace the coordinates. save it.
7. done! if you open kicad again your polygon should look similar to this:
as mentioned earlier in this thread you need to connect or place a component inside the polygon to be able to fill it.
All credits here goes to @Joan_Sparky for making this cool script.
My situation was not similar to yours, but since I came here googling arced/curved ground planes I just want to show what the solution was for me, so no one in my situation thinks he needs scripting to solve it.
I basically had a square outline with curved notches, and was looking for a way to trace the outline curve with ground plane. Turns out I got away with just drawing the outline on the absolute outline border and the ground plane was restricted to my board outline and therefore curved itself.
That is normal behavior⌠you can even do this (without the help of the edge.cuts layer):
But it will be pretty tiresome to draw something like the OP needed with different edge radii and other shapesâŚ
Hi,
Iâve been using the python script KiCAD_CopperArc.py to create some round tracks. Iâm using python 2.7.14 and kicad 4.0.6. The problem is that the tracks I generate are shown by pcbnew but donât belong to the net I am assigning them, they are all inserted to the ânet [] (0)â, even if in the .kicad_pcb file the net is (net 1).
I tried to change the position of the added tracks inside the .kicad_pcb file from the end of the file to the âsegmentâ section (it seems that the tracks generated by kicad are ordered according to the number of their associated net) but the problem is not solved.
Maybe Iâm not using enough fiddling and determination but I really donât know what else can be done apart from changing the position of the inserted tracks. Do you have any ideas?
Thank you
Does your kicad_pcb file have a netlist assigned to it, or is it a blank/new one?
You need something like this to appear in that file, then the net assignment should stick:
....
(subtractmaskfromsilk false)
(outputformat 1)
(mirror false)
(drillshape 0)
(scaleselection 1)
(outputdirectory gerber/))
)
(net 0 "")
(net 1 GRD)
(net 2 SNS)
(net 3 HV)
(net 4 0V)
(net 5 +UB)
(net 6 "Net-(D8-Pad2)")
...
Thinking about it some more, it would help to have a copper track going to a pad with the same net that you assigned.
So the track isnât considered loose and itâs netclass reduced to zero.
If you start PCBnew, a way to get around this is to disable DRC⌠then create that connecting track⌠then save the whole thing⌠and then activate DRC again.
Soemthing along those lines equals fiddeling + determination.
The .kicad_pcb file had a netlist assigned. I solved the problem disabling the DRC and drawing a copper track ending exactly at the beginning of the curved tracks, before the adding of the curved tracks themselves.
Thank you very much for the fast and useful answer!
Another solution is to run KiCommand, but it requires the nightly version at this point.
Works with nightly
WARNING: The nightly version is not guaranteed to produce files that can be opened in the stable version. There is not even a guarantee that one nightly build can open the files produced by another nightly build. (In most cases there is no problem but you might encounter one. Just know the dangers that come with using a development build.)
It can create regular polygons with as many edges as you want to draw. Then you can use the âregularâ command to make it a regular polygon (equal edges, equal angles). At this point, itâs only on drawable layers, not copper, yet. But you can get the points you need from the file after saving. Then maybe change it to a copper track afterwards.
Use âregularâ then delete the segments you donât want. I find 32-64 segments is close to a circle.
Future commands will make creating copper nets possible directly.
I am laying out a circular PCB with a series of twelve pie-shaped wedges, every 30 degrees, for an electrostatic sensor. At first I used Inkscape and svg2mod to create the whole thing as a custom footprint. This used the âfp_polyâ command in the footprint, and I added a small square pad inside each wedge so there would be something to connect to.
This worked great, except that I have parts mounted on the other side of the PCB, and I need to use a few vias to connect to inner layers (this is a four-layer board). Because the footprint âzonesâ are not real kicad filled zones, kicad wonât clear a ring around my vias where they protrude into my sensor footprint, and they will short out. Bummer.
So I found this thread and decided I would be just as well off (maybe better) using proper âfilled zonesâ generated with the poly version of the python script developed above (thanks!). There are just two problems:
-
My board is 10 cm in diameter, so the 32-segments-per-360-degrees limitation is a real problem. The python script makes a really nice pie-wedge-shaped zone, but as soon as kicad refills it for any reason, the nice curved edge goes away and is replaced with a very jagged edge.
-
I want to push the copper as close as I can to the edge of the board. AFAICT the only way to accomplish this is to change the global âclearanceâ parameter for the zone, but this also affects the clearance to tracks and vias, which, unlike the board outline, I do need to be careful of.
Issue #1 is exacerbating issue #2, because the clearance to Edge.Cuts is determined by the joints in the line-segment approximation to the curve. Because that is such a crude approximation on a 10-cm circle, the actual clearance from most of the copper to the board edge ends up being considerably more than the nominal clearance.