What I did to accomplish the task I needed is slightly involved, as-in find a way to thread the needle type involved, so I’ll document the process here.
First, I require the sheet to be “Standalone” so I could enter component designators from the original design, which might conflict with other sheets still in various stages of work in the KiCad hierarchy. Then I need to transfer original design BOM information using the Symbol Fields Table tool. This must be done, so I can export a KiCad BOM for comparison with the original design, looking for discrepancies. This must be done so nothing is missing from translating the original design, so it can be picked up and modified for the current application. As a final step, I like to run KiCost on the result to make final tweaks so everything works. This corner of the design doesn’t require SPICE, so that step is left out. During the time we’ve spent discussing this topic, I’ve completed the current B-Size sheet following this process.
To get the Standalone sheet I somewhat followed @ML9104’s original suggestion. To do this I had to follow these steps, exactly:
-
Open the original KiCad project file for the hierarchy in KiCad, and no other files. This loads the component information needed to prevent the “eeschema Warning Dialog” I showed earlier.
-
Open MS File manager to the project location. Double-click on the file which needs to be worked on standalone. It will open this time because component information is already loaded from the prior step.
-
Now create the “KiCad Standalone Project” .kicad_pro by selecting File->Save As… in eeschema
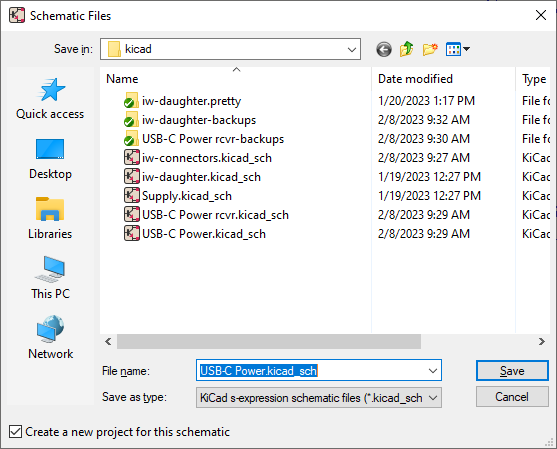
… and notice “Create a new project for this schematic” is selected in the bottom left of this dialog. This will create the Sheet.kicad_pro file needed for the operations described in the second paragraph of this message.
-
From here, double-click on the newly made Sheet.kicad_pro which now shows up in the Main KiCad project dialog
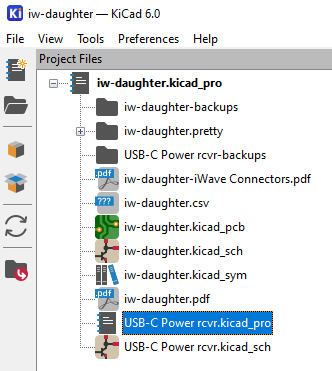
-
Notice the file list is resorted and the schematic for this KiCad standalone effort is at the top of the list
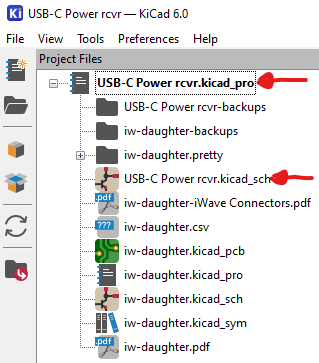
This single page can now be operated on as described in the second paragraph of this message.
The problem with this approach is the page is literally standalone. The component designators stored in the Hierarchy.kicad_pro file don’t get updated with edits in this document. This is a relatively minor inconvenience for all the operations I need to perform while developing this standalone schematic. Once the standalone is complete, I suspect I can copy the entire schematic with modified component designators, open the Hierarchy version, and paste the new data into the Hierarchy. The schematic will already be up-to-date, because after all, we’re working with the same file/page in the design. So all we’re really doing is copying component data fields from the Sheet.kicad_pro to the Hierarchy.kicad_pro.
From here, I can use Annotate tools in the Hierarchy work area to perform the operations described by @paulvdh to clean up the last 10% of the job, which I usually report as “System Integration”. In my experience on many of these types of jobs over decades, 10%-15% is about accurate when reporting schedule milestones. Schedule milestones are needed by Program Managers, Managers who are trying to figure out schedule, cost, manpower, and next project planning while I do the engineering work. Other downline groups like Manufacturing, Test, Marketing like to know when they can expect a finished design too. So this drives a lot of work outside my direct responsibility.
For hierarchy annotation, a more flexible approach might be to use a number mask to define which part of the component number is the “page” and which part is the original component. This way, I may be able to keep the original page component designator values while overlaying page number information to the original component values. The concept is similar to using a Netmask in Internet IP numbers… you know the 255.255.255.0 or /24 notation. This describes what part of the number is the Network part, and which is the Subnet ID/Device part. This will make it easier to trace inherited designs and compare to the submodule design used in the system. i.e., R101 might refer to page 1, component 1, or R101 depending on the component number mask. Or R1001 if the mask is set differently to allow more than 99 different R’s and C’s in the same design page. A simple “PPPNN” mask notation with the option to only overwrite/update page information might be useful. Or just a single digit number field 1-9 which describes the location of the Page/Number boundary location. I only use A and B size pages in my designs because we no longer have C and larger page plotters or ammonia based blueprint machines for schematic copies in a document center. Most office (and some home) locations can print Letter(8.5x11), Legal(8.5x14), and Tabloid(17x11) size pages. For anyone asking why you’d need more than 100 R’s on a B-size page, think processor bus termination for 64-bit or 128-bit wide buses needing high speed design treatment for transmission line waveform integrity on a bus.