I see you spent time creating the Bits and added the Tags to the PCB-shape. Good Job! Be sure to save the Tools to a backup…
Whiskers and Rough edges can be controlled by Speed and Depth of cut (in our PM’s I showed my ‘Results Summary Test’ panel. It was for Poly-PCB’s (not FR4) and I showed the Speeds and Depths but, it does not inform you about Step-Down - that is also a key to having clean edges.
The PCB material - FR4 Vs. Poly: they are not the same beast. Poly mill’s clean. FR4 requires finesse.
Your effort should include Milling Tests for each Bit with focus on Speed and Depth and StepDown.
When I mill Poly PCB’s with a 0.7mm bit, I do a; full depth = stepdown = 0.5mm at 110mm/M and they are perfect. If any cleanup, I use a Toothbrush or fine stiff-brustle brush. No Toothpaste required 
I don’t like milling FR4 because the Fabric’s fibers soak-up and wick the cleaning Water, Alcohol and Tinning solution. Hasn’t been a problem yet, but worth mentioning…
I have Milled several PCB’s using FreeCAD to get the G-Code - mostly to ensure my posting stems from personal experience, which includes many other Milling projects unrelated to PCB’s.
When I Mill PCB’s, I use CopperCAM (an Excellent, very Excellent program for PCB milling and, sometimes I use it for Guitar pick-guards - (think Big PCB with no traces/pads - just the Shape).
I enjoyed helping you and glad you posted the results.
Those ‘Slivers’ (the narrow islands/etc)… if you draw the tracks, the Bit-diam… etc, you may see why some islands appear. You can use the Adaptive-Clearing profile tool and other approaches…
G-Code snippet:
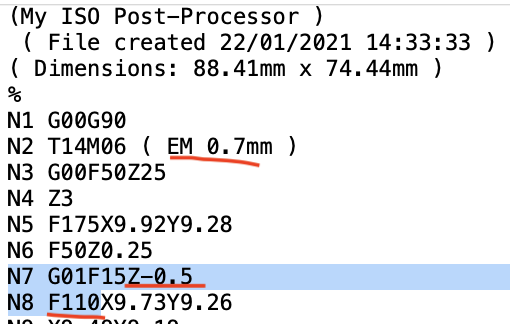
Referring to my Video, this is the Milled PCB from the 1st posted Milling video and, ironically, it’s FR4. You can see the Woven Fabric telegraphing it’s pattern through the Tin Coating. Note the clean edges… some, minor rough edges that I didn’t fuss about cleaning (mostly on the PCB area for removal…)
This is a Poly PCB (Stepper Motor Controllers) - nice clean edges