Sorry, forget that. I had not looked closely enough and had not seen your intermediate PCB connection thing. Euhm, you probably added that later…
Well, it’s one way to do it, but at the price of an extra PCB, and the cheap fabs usually charge based on the amount of PCB’s. You could overlap the PCB’s and then compensate by the distance between the LED’s and the PCB, but that looks ulgy. I would probably just use edge connector like pads and then just solder wires directly over it, or use the square 0.1" headers, lay them flat on the PCB and solder them on both ends. Those steel pins are quite strong.
That is a point of concern. Connector placement is a simple factor that has an surprising big impact. Compare putting the power connector in the center of the PCB compared with at the end of it. When the connector is in the center, you halve the copper length (and thus resistance) to the end, but also halve the amount of current through the track, so that is a reduction of voltage drop by a factor of 4. the tracks passing the power between the PCB’s could also quite easily have been made much wider.
When opening the project, KiCad complains about a missing rescue library. It looks like you fixed the schematic symbols to use a “01_Devices” library (Which is missing) but just forgot to remove the rescue library from the project’s lib table.
There are lots of overlapping texts, such as:
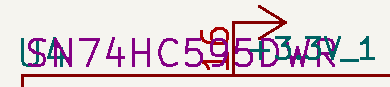
The symbol of the 74HC595 is wrong. Pin 9 is not an inverting pin. In the datasheet it does not have an overbar but an apostrophe. It just bypasses the output latch but does not invert. (The standard symbol in KiCad’s library for V6 is correct). I also don’t like putting the QH’ signal in a row with the other outputs. An empty line here would have made it much clearer this pin has another function then that “group”.
In the schematic you have left the center pin open, but on the PCB they are connected to GND. It’s a bit confusing to define these symbols with a GND pin. Putting pin 1 in the center is also a bit unusual.
What is the size of these capacitors? 100n or 10u?
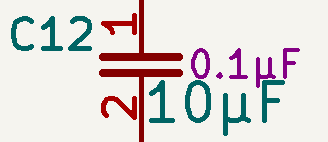
LED’s without series resistors?
Why put al these shift registers rotated on the schematic, and then combine that with the zig-zag bus? I would have put them just next to the LED’s in a straight line, even though that goes against the convention of maintaining a left to right signal flow. It looks like an lot of extra work to draw it in this way. I guess you redrew that section 3 or more times…
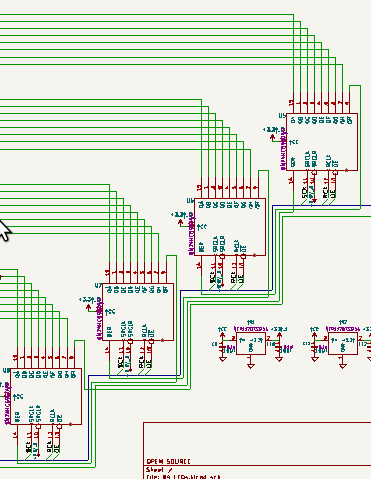
I’m also (unpleasantly) surprised by the PCB itself. The routing looks quite haphazardly without a decent GND plane, and putting the shift registers on both sides of the PCB is a bit of a nuisance for manufacturing.
Why put those buffer capacitors in the far corners of the PCB? They look mechanically quite fragile. They are also by far the highest parts on the PCB. I would have put them further from the edge, kept their legs a bit longer and laid them flat on the PCB (could have added some glue too).
I would have turned the PCB 90 degrees. That fits much better with a my landscape format monitor, and thus results in less zooming during PCB design.
But in the end, who am I to complain? It’s your project and if it works for you then that is the main thing, and you are of course free to ignore anything and/or all I have written. Quite a quirky project indeed.