We need to know what the component is that you want to use
Your explanation is a bit confused. You could make a few screenshots of what you see in kicad and annotate where the shorts are. Or a photo could also show this. I suspect that you did something slightly wrong and your workaround might not be the best option available.
Yes, I agree, but when you order components from China you don’t know exactly what you receive. The fact, I’m using standard module from Kicad V5.0.1 for a RGB Led, at the end, it’s very difficult to sold manually one by one.
Thank you Rene, nothing is confusing because the pellets are too close and the hole for drilling pines are too big. So I have to check one by one each weld, and despite everything, there are still short circuits that are difficult to find. I made pictures.
A picture would be great, I am trying to guess why a plated hole causes shorts. This must be a very strange part.
I avoid what amounts to single layer board as the solder joints are fragile, even worse I guess with lead free solder
Here are some pictures of the real PCB, you can see a very short distance between the pads!
-
When applying the weld, a bridge can easily occur.
The first think I reduce the drill size, actual is 1mm to 0.8.
The footprints you use are for parts with much larger leads. Reduce the drill size and pad size and you should be ok. (Check the datasheet of your device and see what the maximum size of the lead is specified to be. Add a bit to that for solder and the tolerance of your drill sizes and you should arrive at something closer fitting your part. More details on drill size calculation see: Tutorial: How to make a footprint in KiCad 5.1.x (From scratch)?)
Hi Rene, yes that’s I’m doing reducing drill from 1mm to 0.8mm and pads size
Reducing pad sizes will definetly help for your next patch. Using a bit of extra flux combined with a minimum amount of solder will allow you to solder your current patch without trouble. (If you can not solder these huge things forget about soldering any modern integrated circuit.)
And buy good cleaning equipment. Using flux can create a sticky mess that makes it easy for small specs to stick where they should not be. (Like the small metal spec seen in one of your pictures)
Looking at your photos, even 0.8mm is a bit high. LEDs are particularly sensitive to soldering damage, so oversized holes are asking for cooked LEDs
Check your manufacturers requirements for minimum rest solder ring (or annular) as this rule might be violated by your new pads.
A photo might not be the best thing to base this on. For example the knightbrigt LEDs used as the reference for the original footprint have a tolerance range of -0.1/+0.25mm on the leads. ordering a new patch might result in being unable to even get the LEDs in if you decrease the hole size by too much (especially if you also have the combination of getting your holes on the small side of the tolerance range.)
We would need the parts specification documents to make any call on that one.
for reference the knightbrigth pdf https://www.kingbright.com/attachments/file/psearch/000/00/00/L-154A4SUREQBFZGEW(Ver.11A).pdf (drawing is on page 1)
You’re right, ideally it should be better to use the manufacturer’s specifications of Leds. Unfortunately, I do not have them.
So, in the meantime, I made snapshots of my RGB cube (it’s a Kit that I’ve been working on for a while now), I remove one led and here’s what it looks like:
RGB Cude:
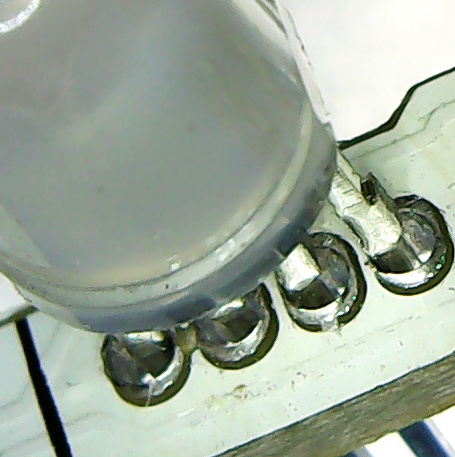
My PCB :
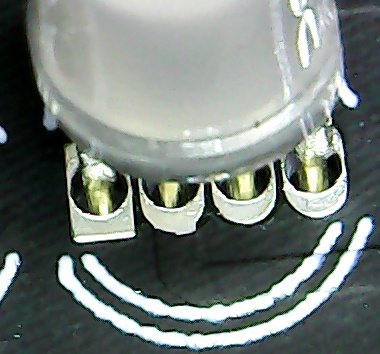
RGB Cube :
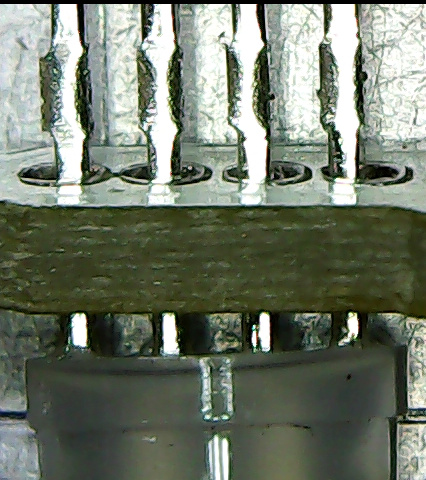
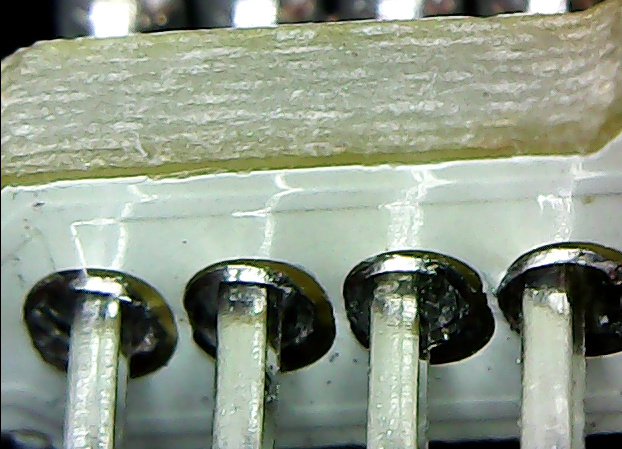
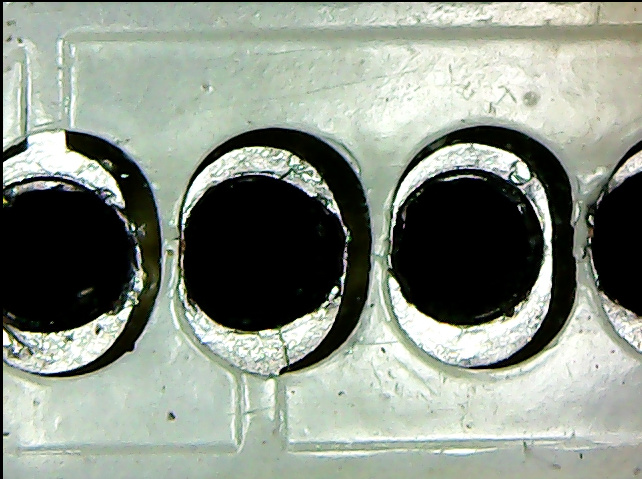
I sold myself this RGB Cube without any problem !
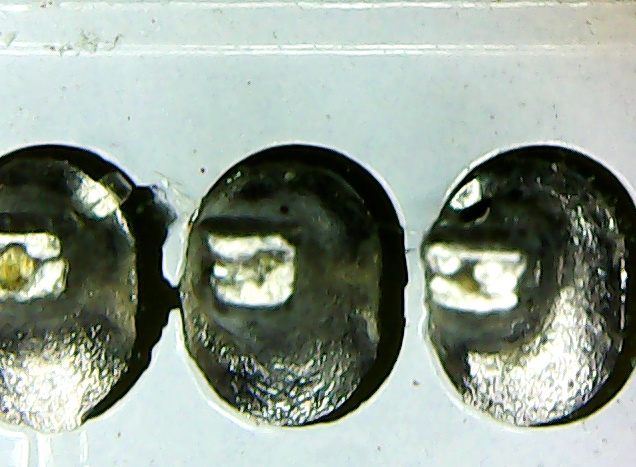
I use same led for both to compare.
Solder Is clean not ? I use good tooling I suppose.
If you are hand soldering think about off setting the holes in the pads so that you do every other one from the opposite side. I also make them a little longer. This isn’t an ‘inline’ example but it should get the idea across.
Thank you, it’s not visible on the 3D representation, but I moved, for the diode in line, an external drill on the left and the other on the right to minimize the risk of over-welding between the pads, I hope this help.
How many of these LED’s do you need to solder?
Is it hand assembly, or automated?
With components like these it is a very big advantage to have plated through holes.
Without the through hole plating you need a “round” solder fillet between the LED pins and the PCB, which easily accomodates short circuits.
But if you have plated through holes, you do not need any round solder fillet on the outside of the PCB. If you only fill the “barrel” hole in the PCB it is enough.
You may also want to think about just spacing the holes further apart in a single line.
If you then cut the length of the pins under a 45 degree angle, each pin has a slightly different length and you can insert the pins one-by-one. (Start with the longest, then push the led aside untill the 2nd longest fits, then push harder to fit the 4th pin, etc).
That part suffers from the same problem as TO-92 transistors, and similar thru-hole packages based on 50-mil (1.27mm) pitch. If you are working with 6 mil (0.15mm) minimum feature size - a typical constraint for a board fabricator’s “standard” product - there simply isn’t enough space between the leads! The lead-to-lead spacing must accommodate:
-
The lead’s mounting hole (0.9mm/35 mils - whether or not it’s plated),
-
Plus two annular rings (0.15mm/6 mils each - and could be more),
-
Plus minimum copper-to-copper spacing (0.15mm/6 mils)
It helps if you reduce the hole size to 0.8mm/32 mils, or even 0.75mm/30 mils if you have a high tolerance for risky behavior. (The smaller holes can be a problem for insertion equipment, especially if the lead dimensions tend toward the large side of their tolerance band.) Elongated pads, and offset drills also help but there’s a limit to how much help they can give. That’s why TO-92 parts are often produced with “formed” leads - either splayed out to a wider spacing, or staggered front-to-back, as previously illustrated by @hermit.
Dale
I have thirty soldering LEDs per circuit, manually, the idea of a 45 ° cut does not seem to me a solution or I did not grasp your tip.
This topic was automatically closed 90 days after the last reply. New replies are no longer allowed.