I’ve been experimenting a bit, and I’m wondering what I’ve put myself into 
David has certainly put a lot of time and effort in this thing and the complications of this being avery weird board (compared to normal PCB’s), and current limitations in KiCad make this a very bad board for beginners to get to know KiCad.
When using the “create pads from Selected Shapes” as I originally suggested. the created pad does indeed look ugly, and with big straight pieces, as in the red track in this creenshot from Pcbnew:
However, this is just a drawing artifact, beause if you select the custom pad in the Footprint Editor, and look at it’s properties, and then the tab “Custom Shape Primitives”, you can see they are clearly defined as arc segments:
I’ve also made gerber files of this connector, and in the gerbers there are more segments, with shallower angles, ie, they look more like arc’s, but still have visible segmentation. If this board gets manufactured, it will very likely be OK in this regard.
Another complication I see is that there are very small clearances.
In the Flex connector at the bottom, the clearances between the connector tracks are not uniform, and some are as low as 83um.
Also on other places the clearances are not uniform.
In the center I see 2 circles used as references, but I do not know which is which.
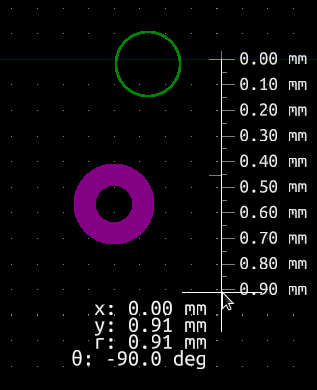
It all resembles hand drawing and guesstimating, and that is not a good sign for aboard with such small tolerances.
With such small clearances you clearly want a reliable DRC to make sure the clearances are met. Which is even more important because of the segmentation i the arcs, which distorts their true shape.
A test upload I did at Oshpark looks like it works if I add a simple rectangular board outline, and move the tracks to a copper layer.
Simply moving the tracks to copper as Setth_h suggests also is not a good idea.
It creates graphical items on a copper layer, and currently KiCad has no DRC for them, and therefore it will not flag your low clearances.